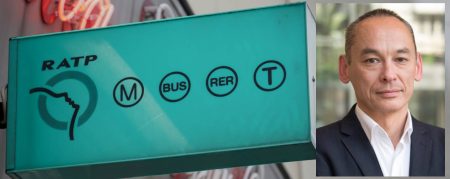
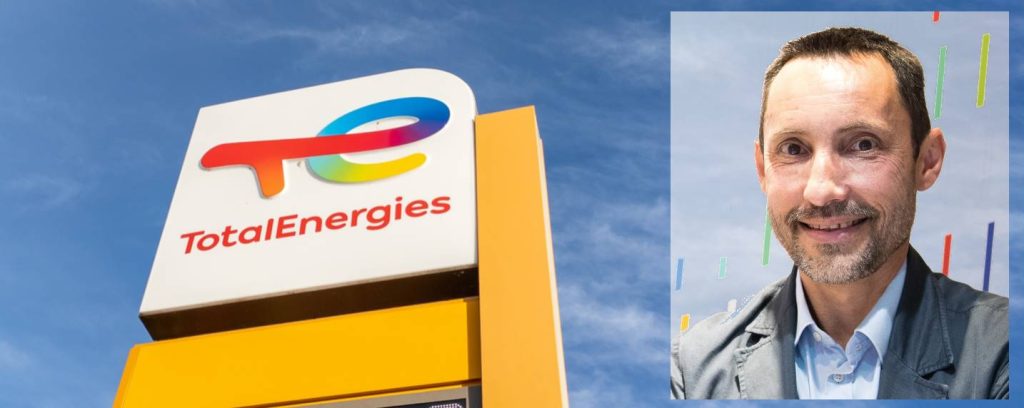
Gouvernance
« Je profite d’une opportunité : pouvoir expérimenter ! »
Par Thierry Derouet, publié le 28 septembre 2022
C’est à l’occasion du salon Viva Technology que nous avons rencontré l’ancien DSI de Total devenu CDO de TotalEnergies. Également patron de la Digital Factory d’un groupe en pleine réorientation, où il est question aussi bien d’énergies renouvelables que de résoudre des problèmes métiers, Frédéric Gimenez évoque avec nous son objectif de création de valeur à horizon 2025 de 1,5 Md$ par an.
Entretien avec Frédéric Gimenez, CDO de TotalEnergies et DG de la Digital Factory de TotalEnergies.
Comment la Digital Factory de TotalEnergies s’est-elle montée ?
Nous avons lancé notre activité en mars 2020 en plein confinement et en mode distanciel à 100 %. Pour démarrer vite, nous nous sommes appuyés sur des ressources externes grâce à un partenariat avec Accenture, ce qui nous a permis de commencer à développer nos projets dès avril 2020. À partir de la sortie du confinement, nous avons débuté le recrutement. Nous sommes aujourd’hui un peu plus de 300 dont 160 internes.
L’idée c’est d’avoir 65 % de ressources internes et 35 % de ressources externes. Nous voulons pouvoir garder une flexibilité sur la taille de nos effectifs et sur le sourcing de certains profils de niche. Dans cette équipe, nous avons près de 40 % de femmes (50 % au sein des équipes data) et plus de 40 % de personnes non françaises, bien que basées à Paris.
Qui décide des sujets ?
Soit ce sont les métiers qui expriment leurs besoins, soit c’est nous qui aidons à réfléchir au potentiel que le digital peut leur apporter. Mais la décision qui l’emporte, c’est la génération de valeur pour la compagnie.
En revanche, la valeur, nous acceptons aussi qu’elle ne s’exprime pas qu’en dollars, notamment s’il s’agit de sujets sur l’amélioration de la sécurité de nos opérations ou sur la réduction de nos émissions de CO2 ou de celles de nos clients.
À LIRE AUSSI :
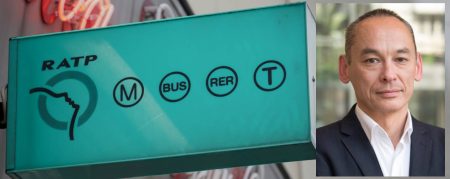
Les sujets que vous accompagnez sont très orientés terrain ?
Oui, effectivement. Nous avions, par exemple, une problématique avec la durée des tests des batteries dans une usine Saft à Bordeaux. Constatant que certains concurrents étaient plus performants, nous avons été sollicités. Disposant des données, nous avons eu la capacité de répondre à leur demande grâce à la data science et avons plus que divisé par deux ce temps, faisant gagner en stockage et en délai de livraison pour le client.
Parfois, nous allons dans une raffinerie où, pendant trois jours, avec l’ensemble du management, nous présentons ce que font, avec le digital, nos concurrents ou d’autres industriels pour résoudre des pain-points. Et là, nous allons en immersion pour ébaucher, maquetter, modéliser, construire et tester des cas concrets. Quelquefois, sur une centaine d’idées émises, nous revenons avec trois cas d’usage que nous allons développer.
Dans quels domaines le potentiel est-il le plus important ?
Un de nos sujets est la maintenance prédictive sur les équipements critiques comme les compresseurs, les turbines. Quand les machines s’arrêtent, la production est stoppée net avec un délai de remise en route assez long et des coûts se chiffrant en millions de dollars.
En plus de la maintenance prédictive, nous réalisons de la maintenance préventive. Un algorithme indique un risque d’incident, tandis qu’un second précise que l’événement n’aura pas lieu avant six mois (time to failure). Sans ce deuxième algorithme, nous aurions stoppé prématurément la production pendant six jours. Nous avons maintenant le temps de trouver une plage de maintenance sans conséquence sur la production et le chiffre d’affaires.
Une telle solution a été déployée en Angola sur quatre de nos plateformes pétrolières offshores. Progressivement, nous augmentons le nombre de machines suivies puis le type des machines.
Quelle organisation des équipes cela suppose-t-il ?
Nous montons une équipe pour chacun de nos projets où nous évaluons les technologies qui vont être mises en œuvre, afin d’y agréger les meilleures compétences. Sans oublier les experts métiers. Par exemple, sur des turbines, nous faisons appel aux professionnels qui interviennent lors d’incidents sur ces machines afin qu’ils puissent échanger avec nos data scientists lors de la modélisation de leurs algorithmes. Nos équipes travaillent en sprints de quinze jours pour livrer la solution par incréments. À chacun d’entre eux une démo est faite aux utilisateurs sur la base de leurs données réelles…
Le cycle normal de développement d’un produit, c’est quatre mois. Les rituels agiles permettent de les réorienter au fil des démos en voyant ce qui marche et ce qui ne marche pas, ce qui est prioritaire. Nous décidons tous les quatre mois de la suite à donner sachant que l’on peut arrêter à tout moment si nous nous rendons compte que nous n’allons pas réussir à résoudre le problème. C’est cela aussi l’agilité et le droit à l’erreur !
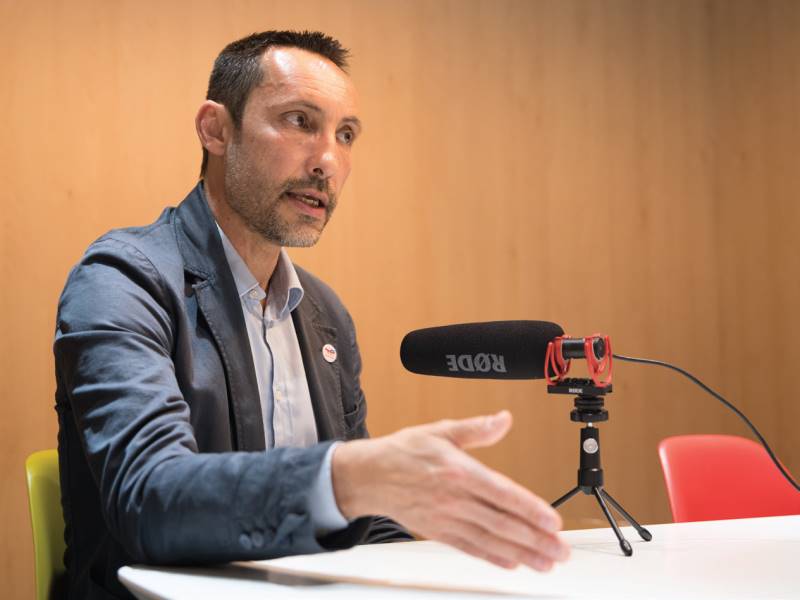
« La création de valeur touche aussi bien les sujets sur l’amélioration de la sécurité de nos opérations que sur la réduction de nos émissions de CO2 ou de celles de nos clients »
Êtes-vous obligés de collecter de gros volumes ?
Nous nous sommes rendu compte que ces grands volumes de données ne faisait pas tout. Selon les raffineries, nous avons entre 10 000 et 300 000 capteurs par site industriel. Avec des historiques sur dix et parfois quinze ans.
Mais ces données ont toujours été utilisées pour faire tourner la raffinerie en temps réel.
Notre objectif, c’est de mieux optimiser le fonctionnement de ces usines en combinant l’approche historique des modèles physiques avec la data science qui se base sur les données et comportements constatés dans le passé.
Et les résultats sont là ?
Nos data scientists essayent de « faire parler » les données afin de détecter des « patterns », pour proposer de nouveaux réglages, de modifier certaines matières premières… Par exemple, nous prenons les mesures des forages effectués ces quinze dernières années (vibrations, résistance, pression de gaz…) et nous y associons tous les événements passés pour, par exemple, prévenir que, dans trente minutes, une tête de forage risque de se bloquer. L’intérêt est immédiat quand on sait qu’il faut parfois plusieurs jours pour sortir une tête de forage coincée.
La data science ne « voit » pas tout…
Vous avez raison. L’essentiel, c’est de « labelliser » les événements réels sur le terrain. Pour la tête de forage, si notre data scientist ne dispose pas de trace de l’événement, il ne sort rien des données. Pour arriver à les relier à l’événement, il faut de bons experts métiers. Le product owner n’est pas le sachant ultime. Il est là pour donner les règles métiers à l’équipe de développement en s’assurant que le feedback des utilisateurs a été pris en compte, et il doit arbitrer et prioriser en permanence.
Mais pour que ceux qui sont sur le terrain depuis vingt ans fassent confiance à un algorithme, il faut les embarquer dès le départ du projet. Cette confiance ne se gagne qu’au fur et à mesure. Il faut également créer des outils adaptés, avec un UX designer, afin que soit prise en compte la façon dont les utilisateurs travaillent. Si un opérateur ne suit pas la recommandation de l’algorithme, il faut que l’on puisse faire remonter facilement la raison de son choix pour que l’algorithme s’améliore. C’est de l’interaction permanente avec l’opérateur. Il faut que ce dernier puisse comprendre la logique qui est derrière le système, et se l’approprier.
C’est toute l’entreprise qui est concernée ?
Il n’y a pas de transformation digitale, il y a une transformation de notre business. Et le digital est un facilitateur de cette transformation. Nous n’allons certes pas supprimer les émissions de CO2 d’une raffinerie avec du digital, mais il doit permettre de les réduire.
Après un incident, nous savons qu’un redémarrage génère du CO2, par exemple. Nous pouvons toutefois le diminuer par une meilleure optimisation de ces séquences grâce au digital.
À LIRE AUSSI :
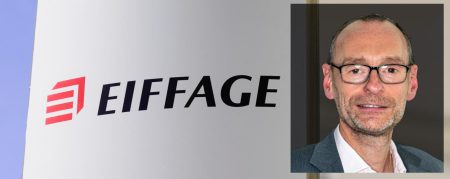
Vu d’un ex-DSI, c’est quoi le rôle d’un CDO ?
Mon rôle, c’est de pousser les technologies pour accompagner la transformation des métiers. J’amène des méthodes, des compétences, des cas d’usages. J’amène aussi une manière d’évaluer les besoins et de bousculer les habitudes, de faire des projets pour aller plus vite et être très orienté valeur, et enfin d’accepter l’échec. Dans un monde « DSI », il n’est pas acceptable. Mais ici, si.
Pour votre Digital Factory, quel rôle joue la DSI ?
Nous sommes les utilisateurs de la DSI. Nous avons fait accélérer la transition vers le cloud. Elle était entamée et allait à un rythme raisonnablement ambitieux. Mais cela n’allait pas très vite. Je peux le dire, car c’est moi qui l’ai lancée.
En revanche, quand nous avons monté la Digital Factory, nous avons été les premiers à décider que nous serions 100 % cloud. Nous avons embarqué les équipes de la DSI qui construisaient les plateformes cloud dans la Digital Factory afin qu’elles puissent disposer d’un feedback permanent de notre part. Ensuite, nous avons commencé à développer des applications « cloud native ». C’est maintenant devenu un socle que notre DSI est capable d’apporter auprès de l’ensemble des équipes applicatives pour tous les types de projets.
La transformation cloud a beaucoup fait bouger les lignes. Mais les plateformes de la Digital Factory sont celles des SI. C’est la DSI qui opère et fait évoluer les plateformes. C’est également la DSI qui négocie les grands contrats avec les fournisseurs tels que Microsoft et Amazon.
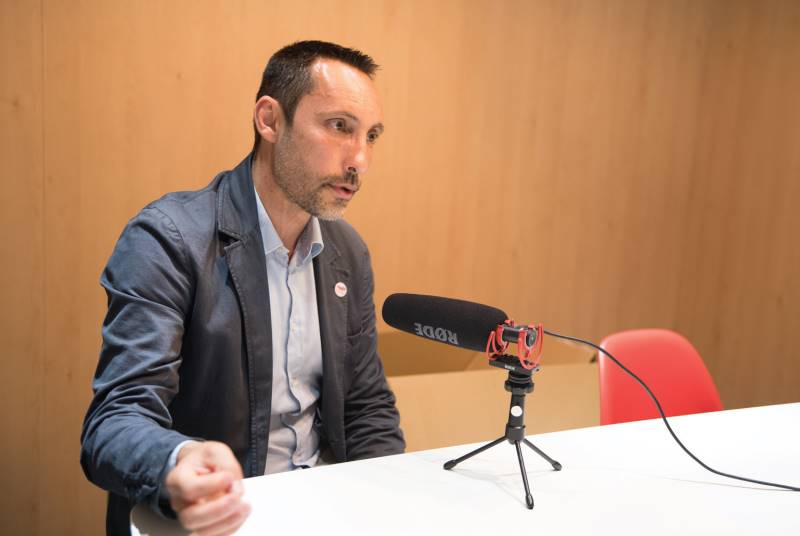
« Nous n’allons certes pas supprimer les émissions de CO2 d’une raffinerie avec du digital, mais il doit permettre de les réduire. »
C’est donc un partenaire essentiel ?
Oui. La DSI nous donne accès aux données. La majorité des données que nous utilisons existent déjà, elles sont dans nos systèmes. En revanche, nos systèmes sont nombreux – 2 000 applications, dont certaines hébergées dans nos sites industriels – et pas toujours ouverts. Nous poussons la DSI à « API-ser » le legacy. Mais nous le faisons de manière raisonnée. Nous ne disons pas « faites tout le legacy », mais « voici les terrains de jeu sur lesquels nous allons jouer ».
Je ne crois pas aux grands chantiers up-front où l’on met toutes les données au carré, tout le legacy en API. Pour TotalEnergies, cela durerait dix ans, cela coûterait une fortune et cela n’aurait en définitive aucun intérêt.
Un CDO, c’est encore un DSI ?
Un CDO, c’est un DSI qui peut dire non et qui n’est pas là pour opérer en 24/7 des milliers de systèmes dans un monde cyber dangereux, ou pour fournir ‒ situation de Covid oblige ‒ en une semaine un environnement de travail en remote auprès de 70 000 personnes.
Notre DSI a un nombre incroyable de choses à faire tourner, 130 pays à gérer, des milliers d’applications, des milliers de prestataires…
Moi, mon métier est, en quelque sorte, beaucoup plus cool. Avec toutefois un objectif qui l’est moins : délivrer à partir de 2025, chaque année, 1,5 Md$ de valeur. Mais mon job, c’est de pousser les métiers jusqu’au bout pour les aider à réaliser leur transformation.
S’entendre avec sa DSI, c’est facile ?
Je parle souvent avec François Tête, notre DSI. Nous nous entendons très bien et nous sommes convaincus que notre collaboration étroite est indispensable pour le succès global de la compagnie. Parfois, c’est François Tête qui me pousse, parfois c’est moi. Mais à chaque fois, nous nous disons que c’est pour le bien commun.
Au départ, François considérait qu’à la Digital Factory nous étions des défricheurs, car nous avions des gens qui avaient des connaissances technos nouvelles qui n’étaient pas utilisées par la DSI. Nous étions l’innovation techno de la DSI. En revanche, côté cybersécurité ou choix des providers cloud, c’est lui qui donne le cadre, il n’y a pas de marge de manœuvre et je l’accepte bien volontiers.
Un CDO amène-t-il la DSI à moderniser le SI ?
Comme nous nous connectons beaucoup aux applications existantes, nous poussons beaucoup à la transformation du legacy. Nous avons milité pour que la DSI porte de nouvelles plateformes API et IoT ainsi que de nouvelles connectivités sur nos sites industriels. La DSI se transforme en se mettant à opérer des objets assez nouveaux dont ils n’ont pas forcément besoin pour leurs activités historiques. Mais cela leur permet de prendre un coup d’avance et de transformer le parc applicatif historique.
« Ce n’est pas juste un changement de nom, c’est un changement de cap »
Qui dit nouvelle ambition, dit nouveaux business. Des activités que le digital entend également accompagner.
Selon Patrick Pouyanné, cette Digital Factory, c’était une question de survie ?
L’idée c’est que le digital accompagne la transformation de l’entreprise. Depuis deux ans, la compagnie a beaucoup bougé, avec un virage vers les nouvelles énergies. Le changement de Total en TotalEnergies, ce n’est pas juste un changement de nom, c’est un changement de cap. Nous passons d’une société « oil and gaz » à une société multiénergies.
Quelle est la place du digital dans cette réorientation ?
La mobilité électrique est une nouvelle activité pour nous avec un digital hyper présent. Le propriétaire d’un véhicule électrique doit savoir où sont les bornes de recharge, si elles sont libres, si ses connecteurs sont compatibles, et à quel prix il va pouvoir recharger sa batterie, en payant avec son téléphone. C’est un parcours quasi 100 % digital. Pour y répondre, nous avons créé Be:Mo, une plateforme qui propose une offre multi-énergies pour les véhicules thermiques et électriques. Via des API, Be:Mo donne accès à plusieurs milliers de stations et plus de 250 000 points de recharge électriques dans toute l’Europe sur des App ou directement au tableau de bord d’un véhicule.
TotalEnergies, c’est aussi du renouvelable ?
Nous travaillons aussi sur le trading afin de prédire les variations de prix de l’électricité en fonction de tout un ensemble de paramètres comme la météo, la production nucléaire, la production des renouvelables en Europe, qui évidemment fluctuent.
Nous aidons aussi à piloter nos 400 sites renouvelables en France (fermes éoliennes, champs de panneaux solaires…) dispersés dans des coins reculés où, comme il n’y a personne sur site, nous travaillons sur du monitoring avancé pour détecter d’éventuels dysfonctionnements, intervenir à distance, anticiper les pannes et fournir l’énergie au bon moment.
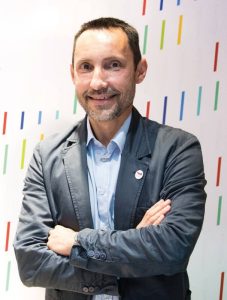
Parcours de Frédéric Gimenez
Depuis septembre 2019 :
CDO de TotalEnergies et DG de la Digital Factory de
TotalEnergies, Paris
Octobre 2018 à septembre 2019 :
Secrétaire général Raffinage Chimie
Total, Paris
Mars 2015 à octobre 2018 :
CIO / Directeur des Systèmes d’Information
Total, Paris
Janvier 2012 à mars 2015 :
VP Information Systems
Refining & Chemicals, Bruxelles
À LIRE AUSSI :
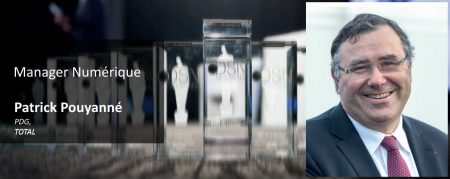
Propos recueillis par : THIERRY DEROUET
Photos : MÉLANIE ROBIN